About thyssenkrupp Dynamic Components TecCenter AG
thyssenkrupp's Automotive Technology business segment is one of the leading suppliers and engineering partners to the international auto industry. The range of products and services includes high-tech components and systems and automation solutions for vehicle manufacturing.
The product range includes chassis technologies such as steering and damper systems and the assembly of axle systems, as well as powertrain components for conventional and alternative engines. In addition, assembly systems for body-in-white construction are also developed, and lightweight car body components in series are produced.
Automotive Technology covers the entire value-added chain, from developing and producing high-performance components and mechanical processing to assembling highly complex systems. Mechatronic solutions with electronics and software developed in-house are playing an increasingly important role.
Services:
Selmo Services
Proof of Concept
Industry:
Automotive Industry
Location:
Eschen, Liechtenstein
.png?width=500&height=250&name=logo%20thyssenkrupp%20(3).png)
Project overview
Project scope
- 359 PLC inputs and outputs
- 6 axes
- 7 sequences with 187 steps modeled in
- Selmo Studio
- 236 zones
- 43 constantly monitored zones
- 265 parameters
- 36 drivers
- 27000 lines of code0 Zeilen vom Code
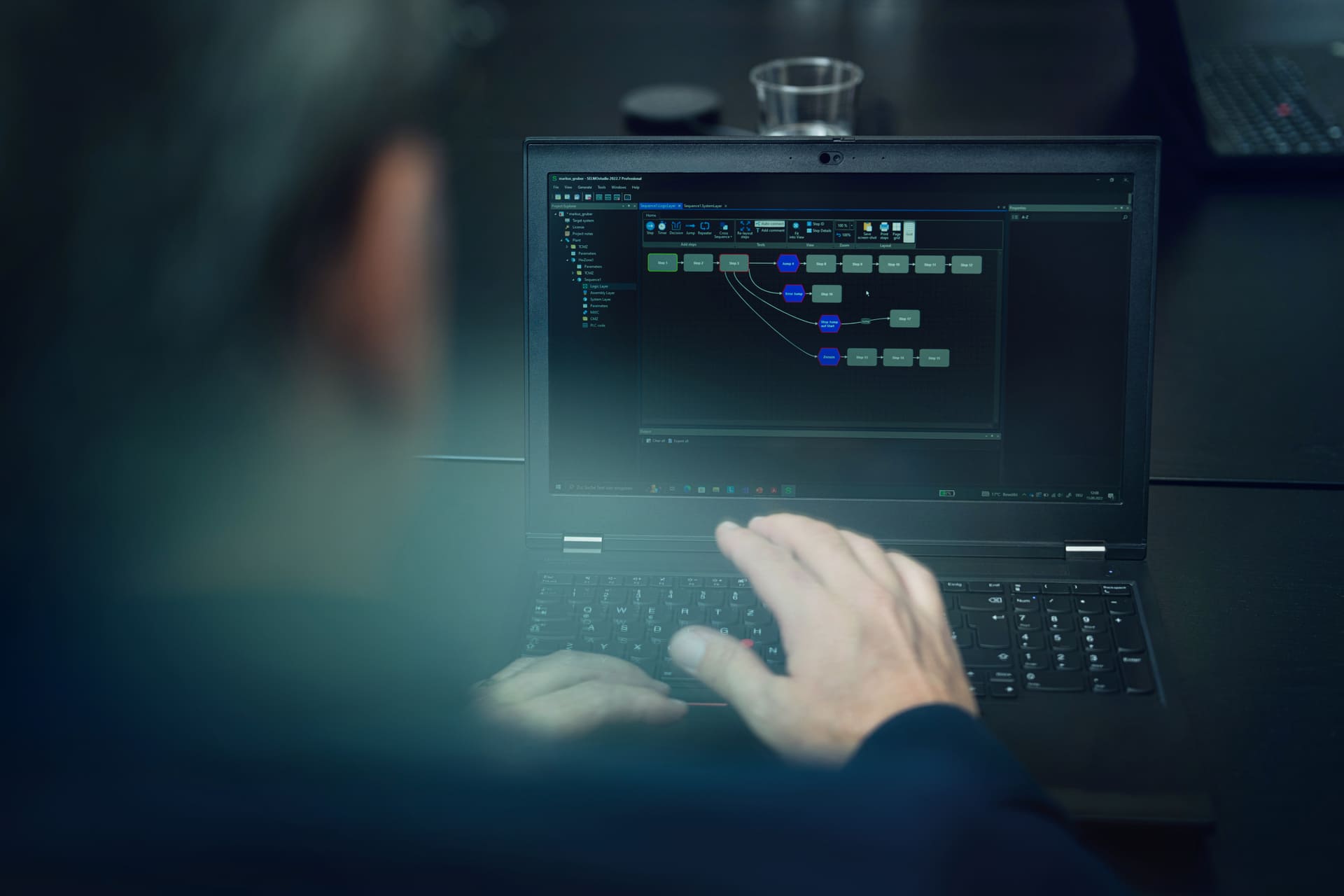
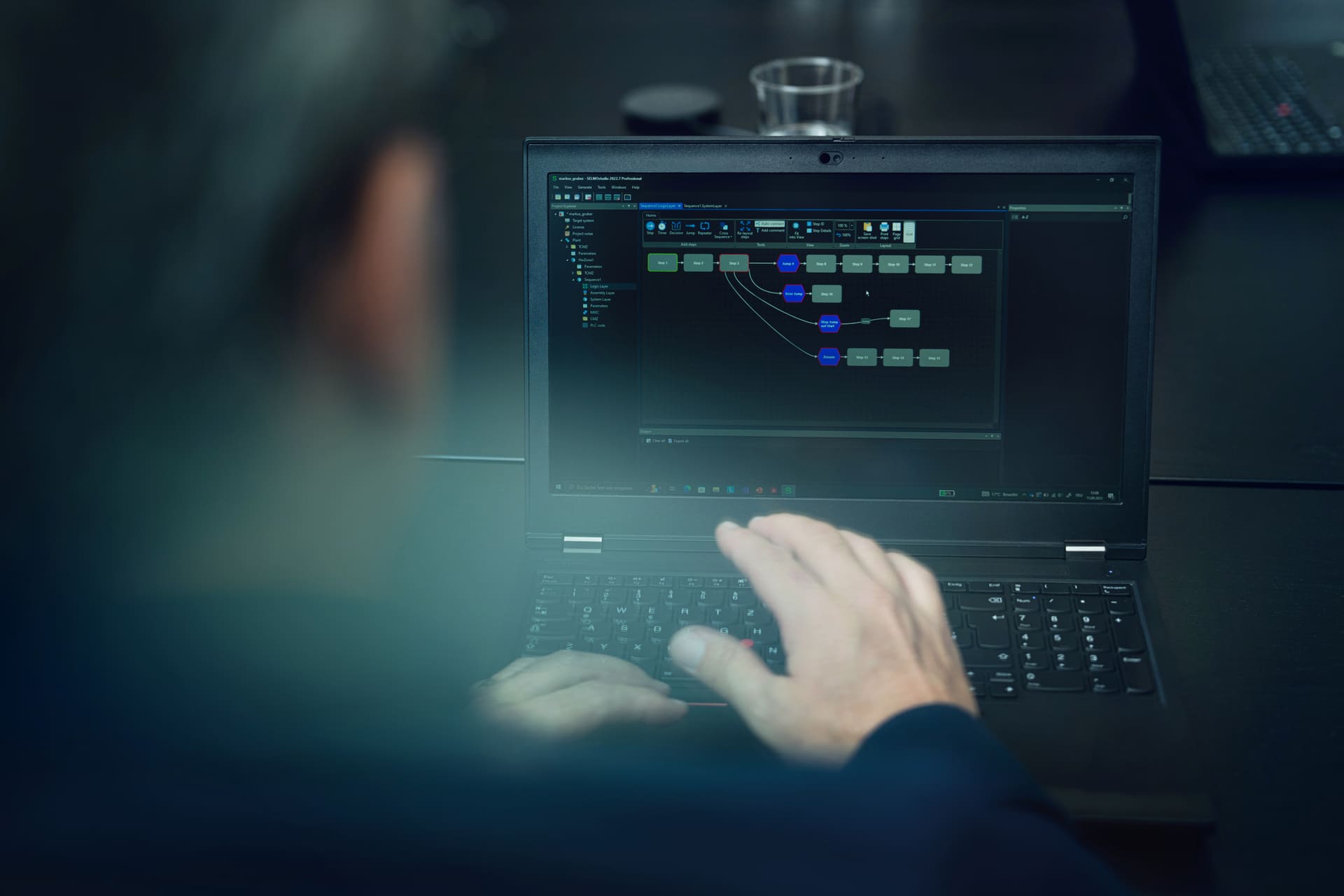
Project timeline
- In the preparation phase, the entire process of the machine was recorded.
- The existing hardware was inspected on-site.
- The process model was modeled in Selmo Studio.
- Then, the process was designed.
- Finally, the plant was successfully commissioned on-site.
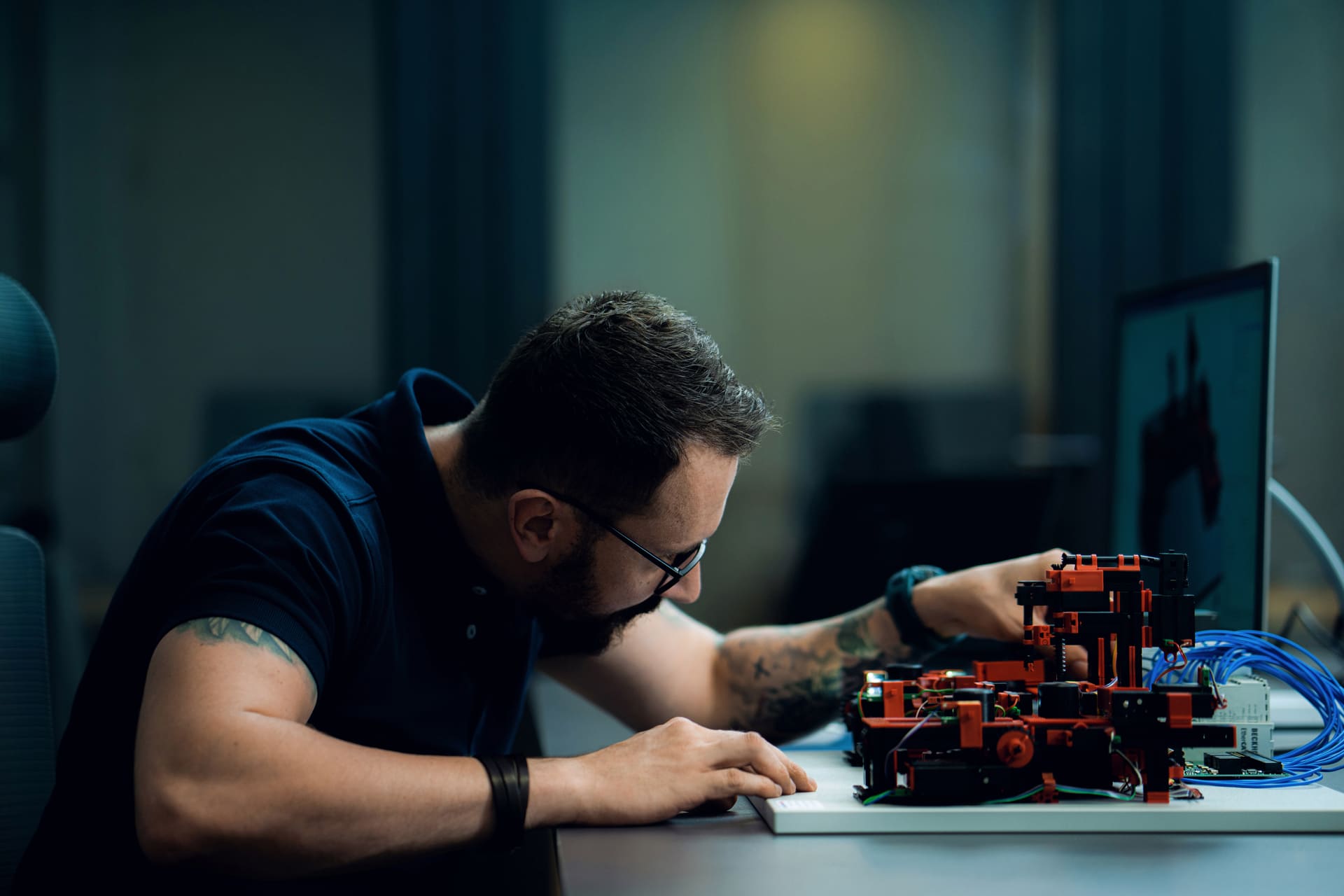

Initial situation & challenges
Selmo carried out a proof of concept for thyssenkrupp Automotive Technology for a cam-setting plant. The project included the entire automation of the plant, from recording the complex process to commissioning the real machine. As a result, the desired goal of building a camshaft was achieved quickly and easily with Selmo.
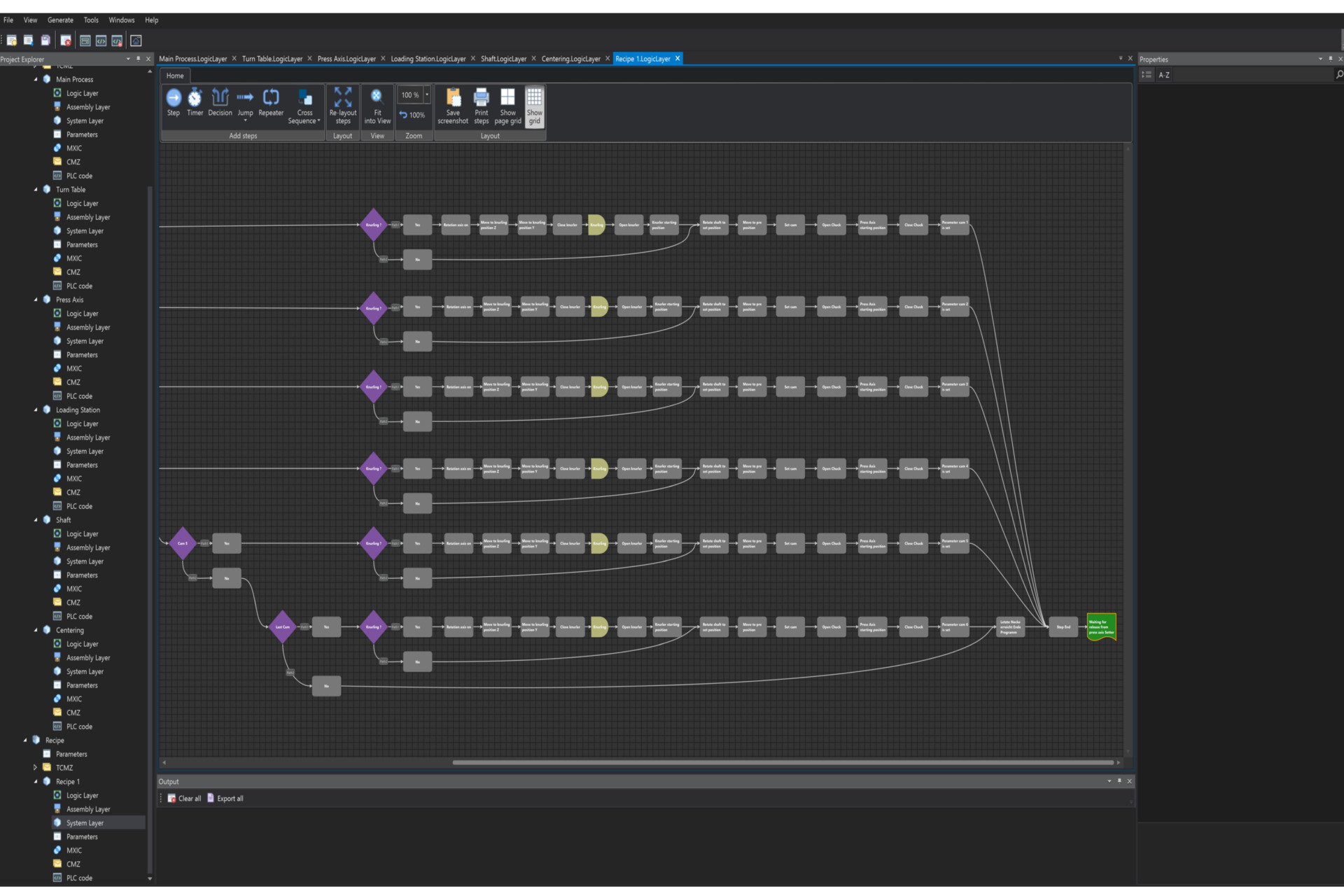
Implementation
In two weeks of preparatory work, a 'step-by-step' documentation was created with the help of videos, pictures, and circuit diagrams to define a clear image of the plant with all the required functions. Then, in a 3-day on-site visit, the Selmo team inspected the existing hardware, such as axes, PLC interfaces, and safety PLC. Meanwhile, the process of the plant was directly modeled in Selmo Studio. After completing the process analysis and documentation, considering all hardware components, and working out all PLC signals based on the E-plan, the plant's design began. This took a week, and the entire plant was ready for commissioning.
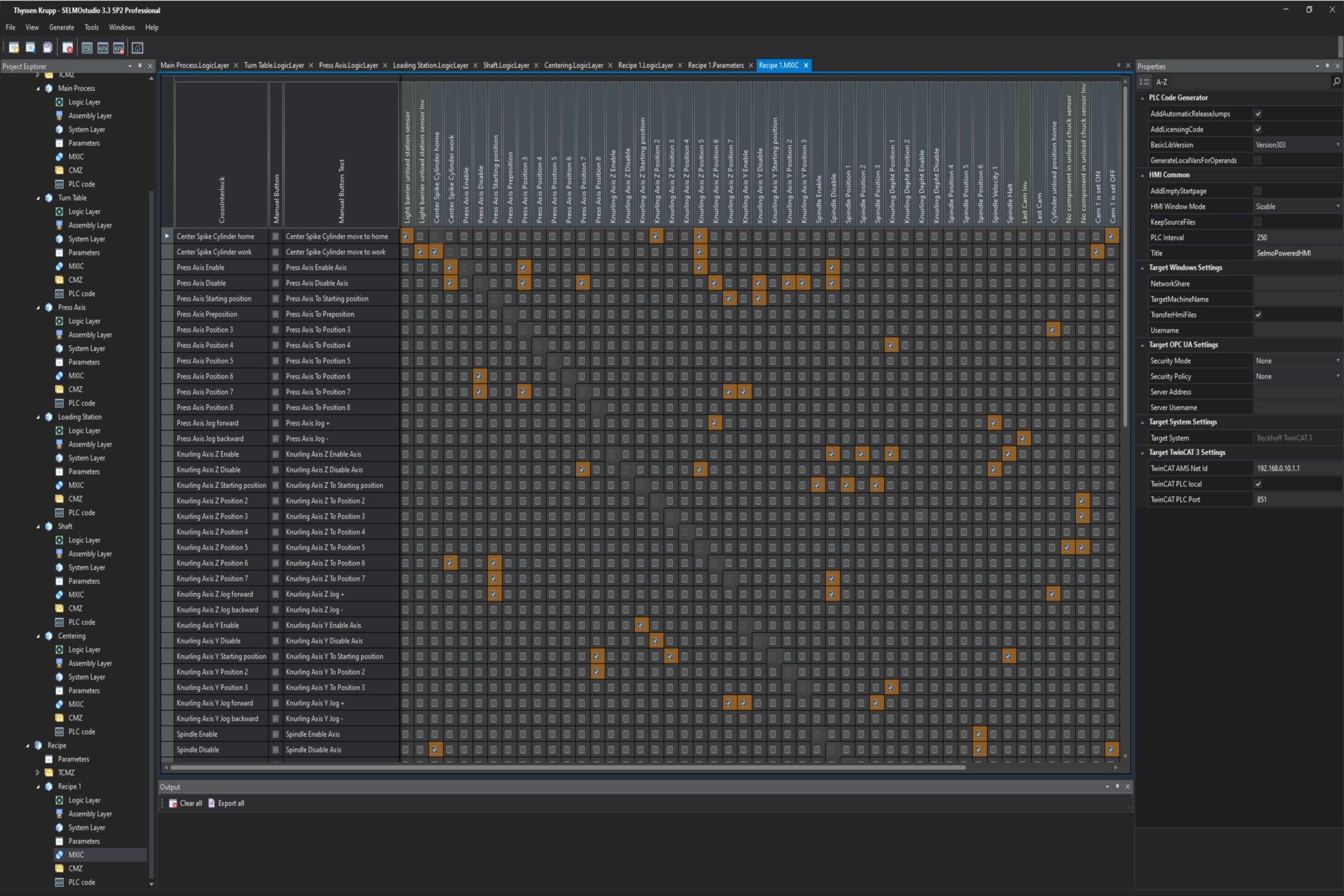
Result & commissioning
To commission the plant with the HMI automatically generated from the model, again, only three days were needed. With the Selmo HMI, it is possible to detect any deviations immediately and, when commissioning, change these in Selmo Studio to import the amendment directly via an online connection to the plant. As with any commissioning, the first step was to control the entire plant in manual mode. These functions are directly included in the automatically generated Selmo HMI and do not require any programming work.