About igm Robotersysteme AG
igm Robotersysteme AG has been a leading welding automation company for over 50 years. More than 4000 robot systems are operating in industrial sectors worldwide.
As a market leader, igm explored the company's digitization potential to shorten the commissioning times of new machines and create a uniform standard for the business.
Services:
Virtual Commissioning
Project Support with Selmo Services
Industry:
Welding Technology & Robot Systems
Location:
Wiener Neudorf, Austria
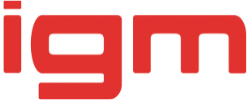
Project overview
Project scope
- 8 Conveyor belts
- 165 PLC in- and outputs
- 11 Sequences with 218 Steps modeled in Selmo Studio
- 380 zones defined
- 12 Constantly Monitored Zones
- 82 Drivers
- 22700 Lines of Code
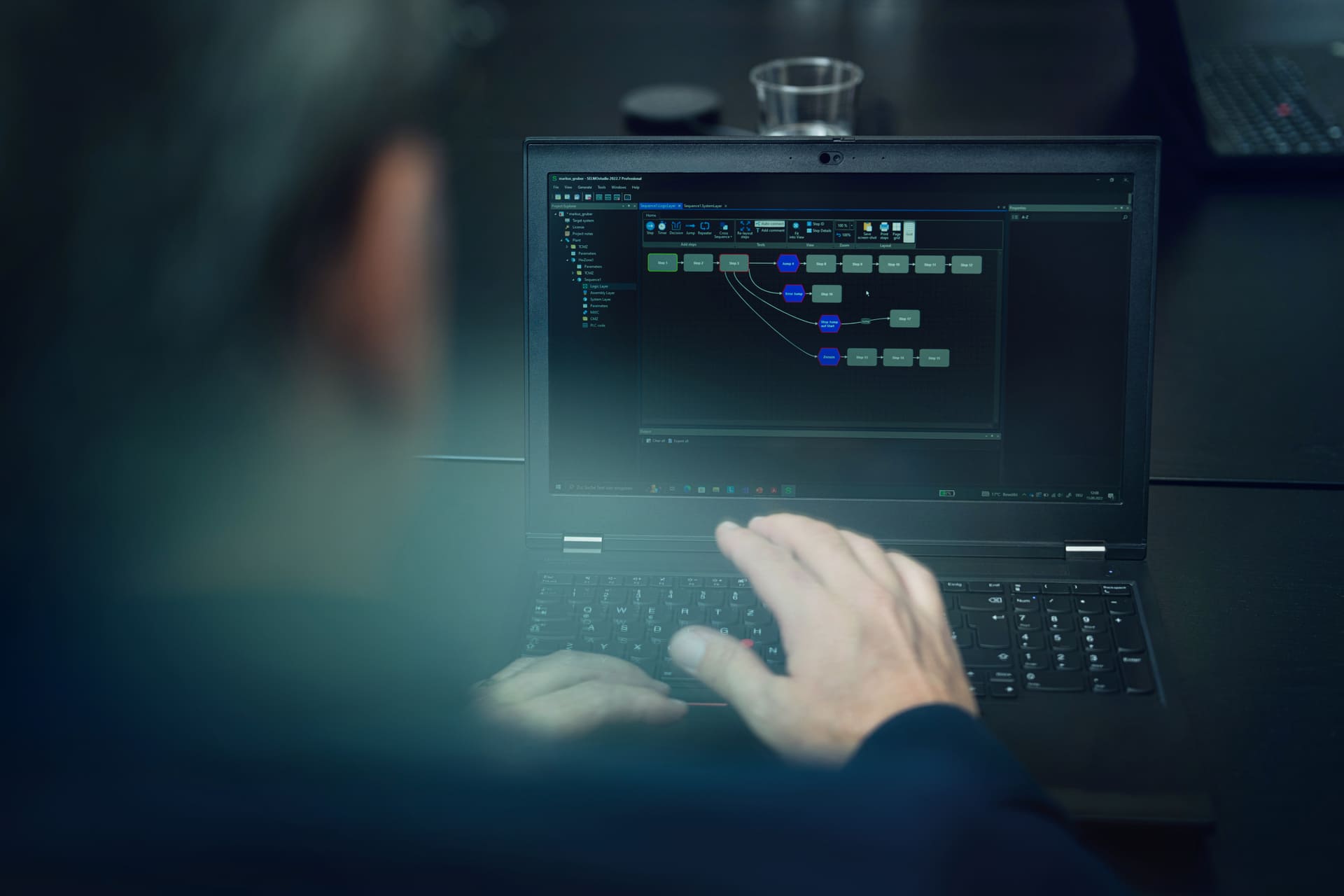
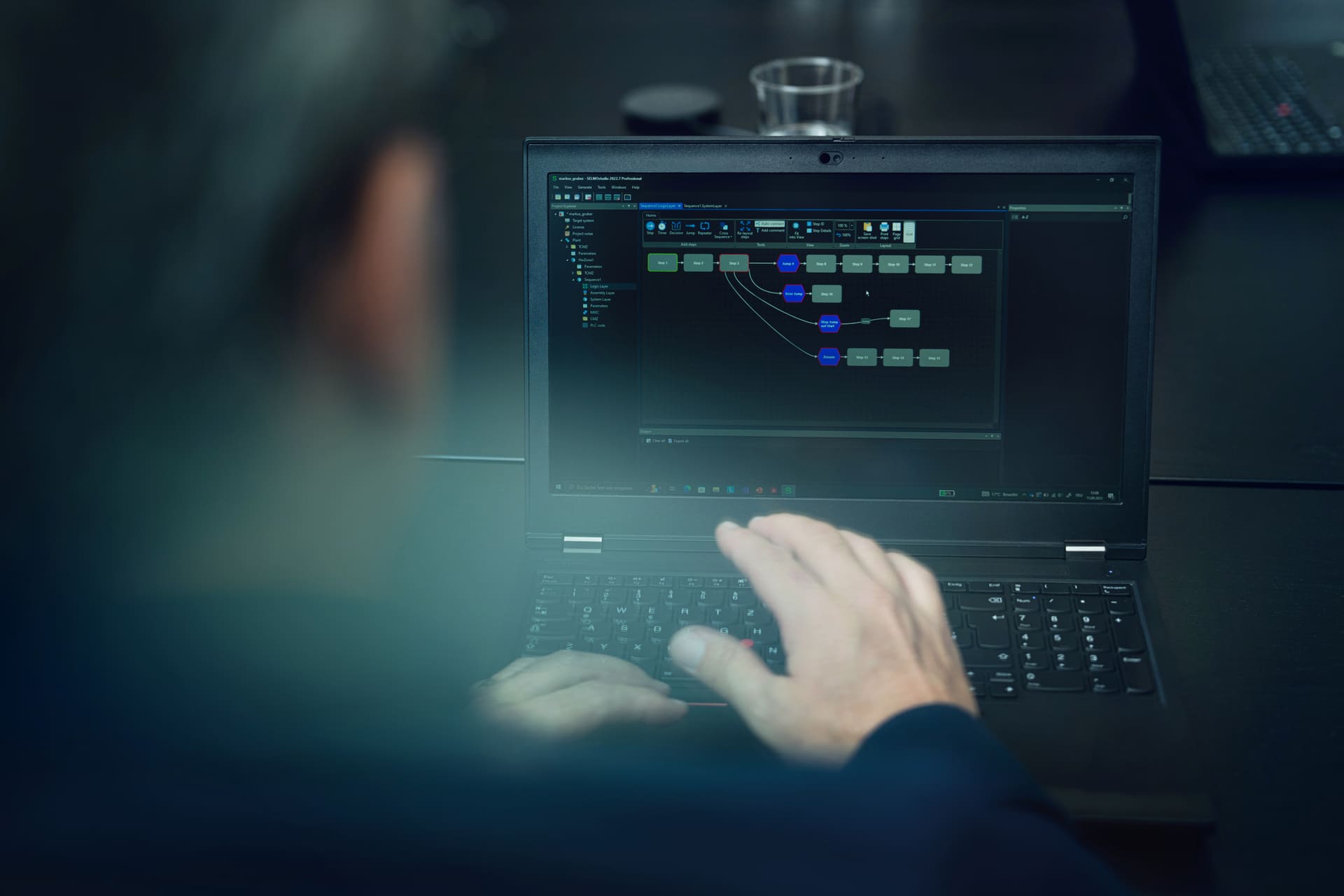
Project goals
- Automation of machine programming
- Speeding up machine commissioning time
- Increased independence from experts
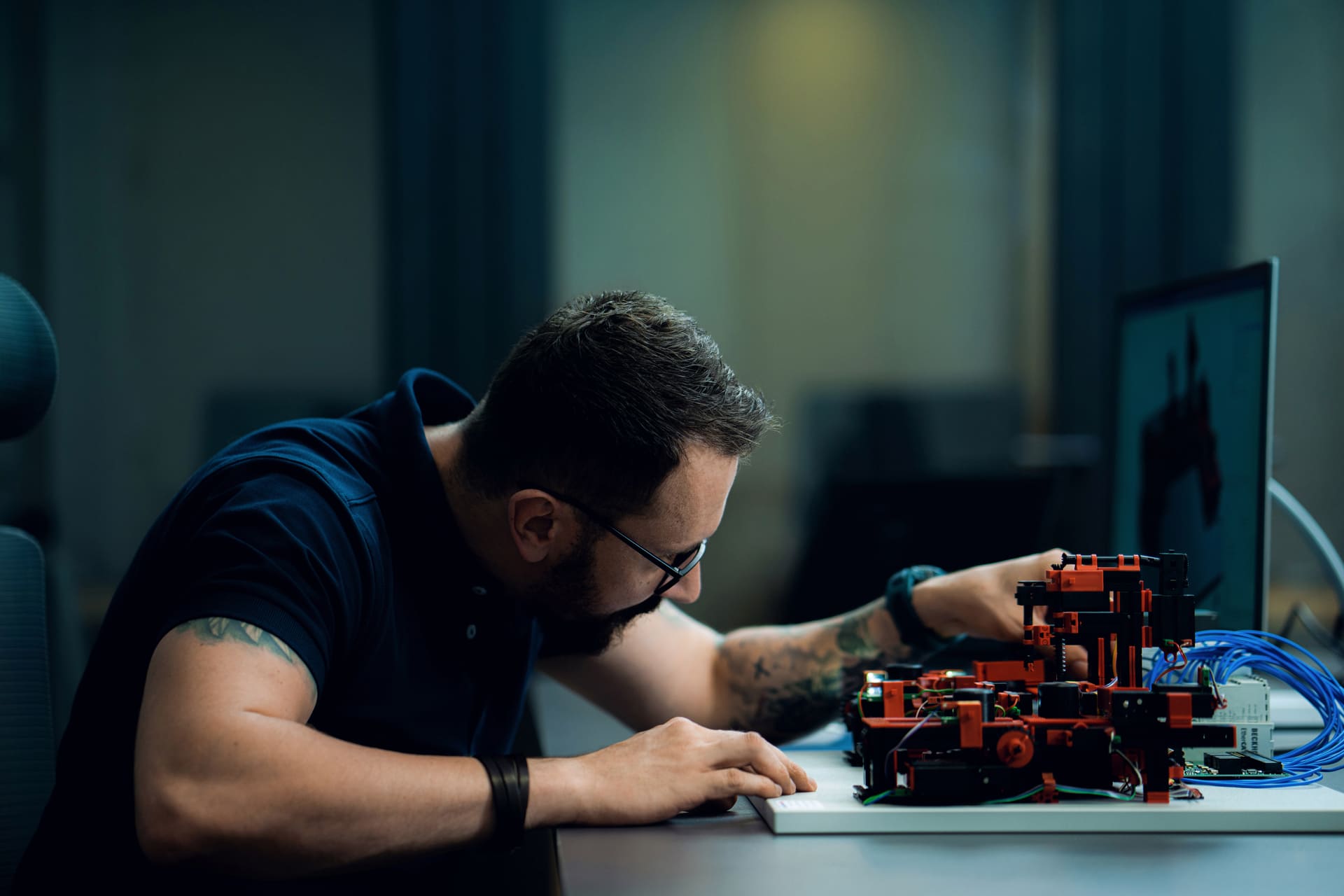
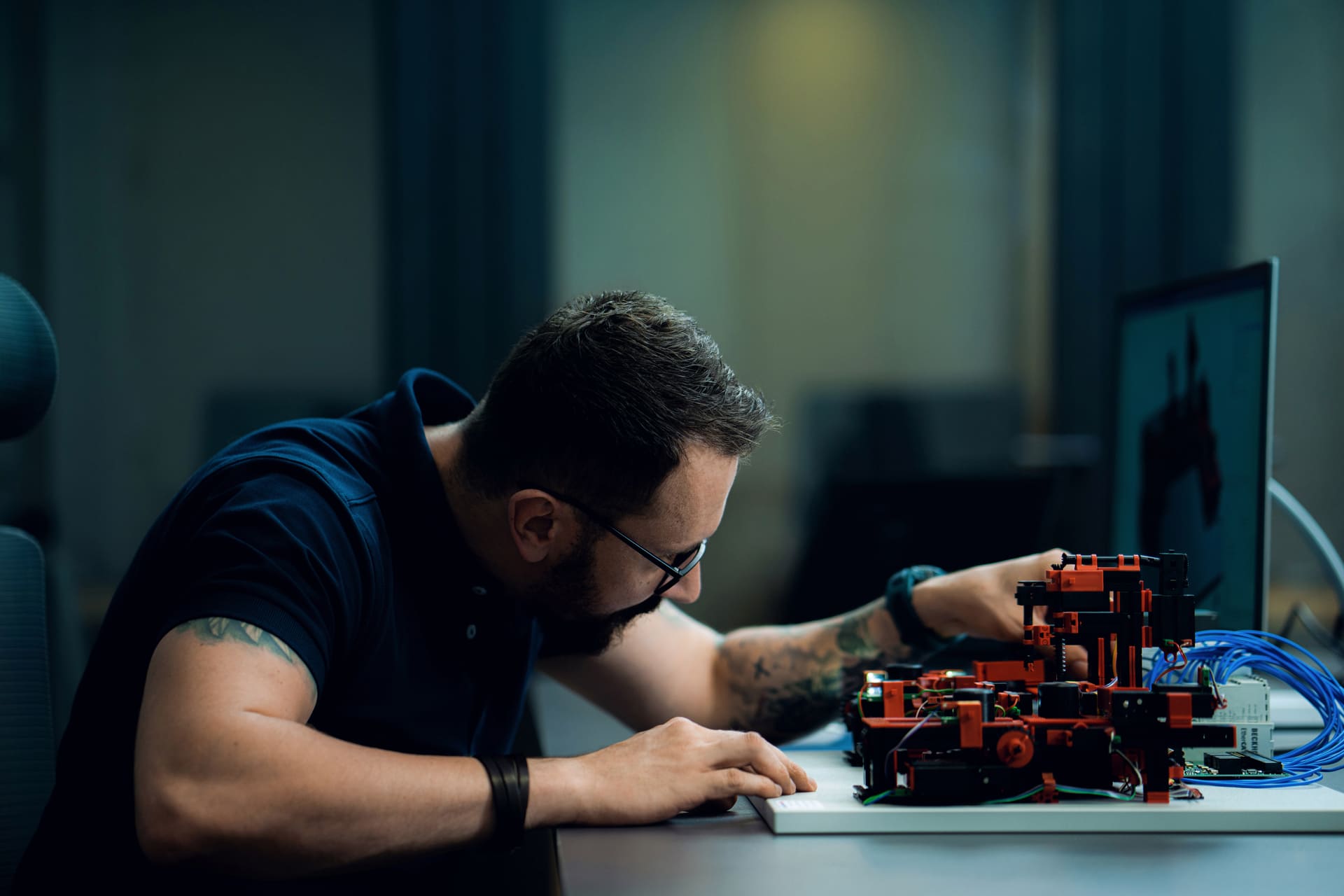
Conveyance for a robot welding plant
Initially, the client provided the required functionality of the machine. Together with Selmo, igm then defined the process. Once done, Selmo Studio converted the process into a model. igm received the clearly, documented process model.
Selmo Studio generated the PLC Code as a next step, and an HMI was directly included. igm provided the 3D model of the conveyor belt. An accurate simulation of the 3D model was conducted, and the link to the target system was established. The model was implemented into the target system, and the virtual commissioning was successfully taken care of.
Only now, igm built the actual conveyor belt, and the electrician executed the I/O check. Upon quality assurance, igm activated the plant.
.png)
"The PLC program was ready before the electrical engineering plan. This was a first in my career, for which I am very proud of."
Otto Auer - igm, Head of Engineering
"The commissioning ran smoothly. The handling of Selmo Studio is straightforward and user friendly."
Patrik Palitsch - igm, PLC Programmer
Efficient workflow through virtual commissioning
When a sensor-cylinder-related error occurred during the commissioning, we knew, thanks to the initial virtual commissioning and the constant monitoring of all machine states in the Selmo Studio, that the error could not be in the program but the hardware. Signal interruptions occurred due to vibrations when the cylinder was extended. This could be solved very quickly.
It took two weeks to finalize the process model and one week to virtual commission the machine instead of the usual three man-months.