About Maschinenbau Brunner GmbH
Acceleration through automated PLC programming: Maschinenbau Brunner GmbH develops and produces machines and systems unavailable on the market. By switching from classic PLC programming to automated PLC programming with the Selmo Solution, their business unit, Brunner Automation GmbH, has considerably accelerated software development for these complex mechatronic plants.
Planning machines according to customer requirements and producing turn-key plants is the expertise of Maschinenbau Brunner GmbH in Wolfau in southern Burgenland. Founded in 2000, the company does not specialize in one industry or machines with specific functions. Instead, it develops and produces special machinery for automotive, building materials, plastics, food, and cosmetics manufacturers. These perform production, transport, and packaging tasks.
Service:
Selmo Support
Industry:
Customized machinery for many applications
Location:
Wolfau, Austria
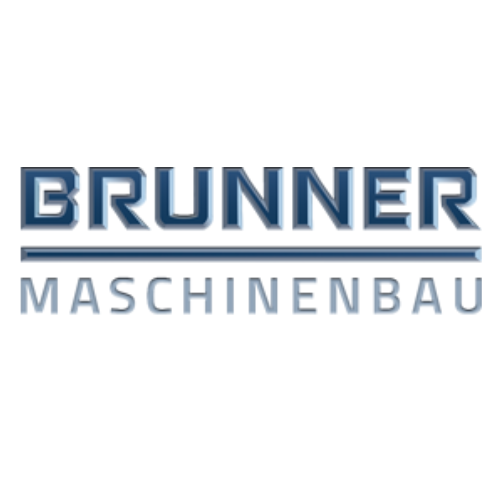
"With the Selmo method, we managed to start at a higher level. It saved us much basic work, estimated at one month."
DI Stefan Knöbl
Managing Partner Brunner Automation
"The Selmo method eliminates the translation of machine behavior into sequential instructions and creates the lines of code automatically."
Christian Wilfing
Automation engineer Brunner Automation
Project Overview
Objective
Development of a fully automatic assembly and packaging system.
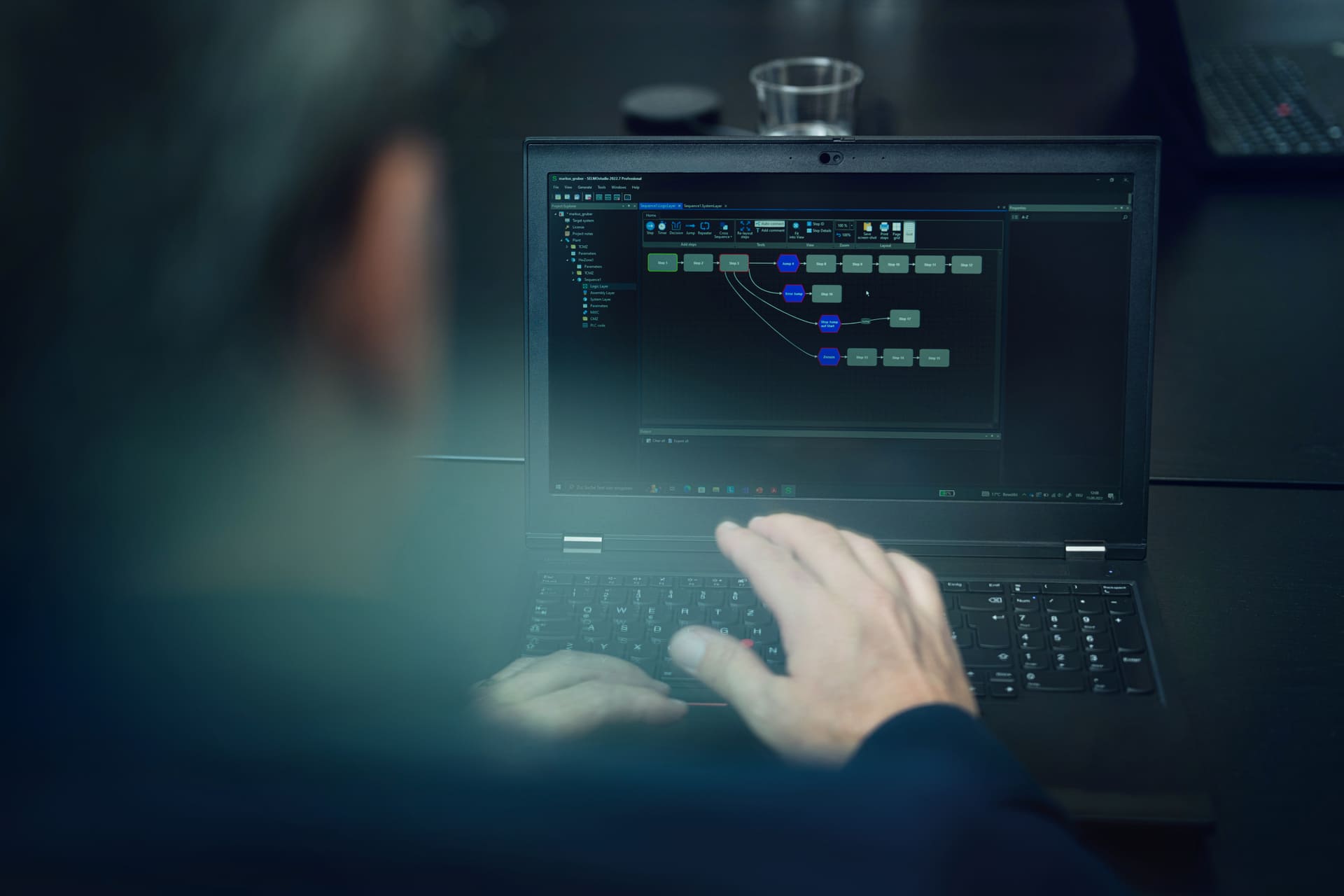
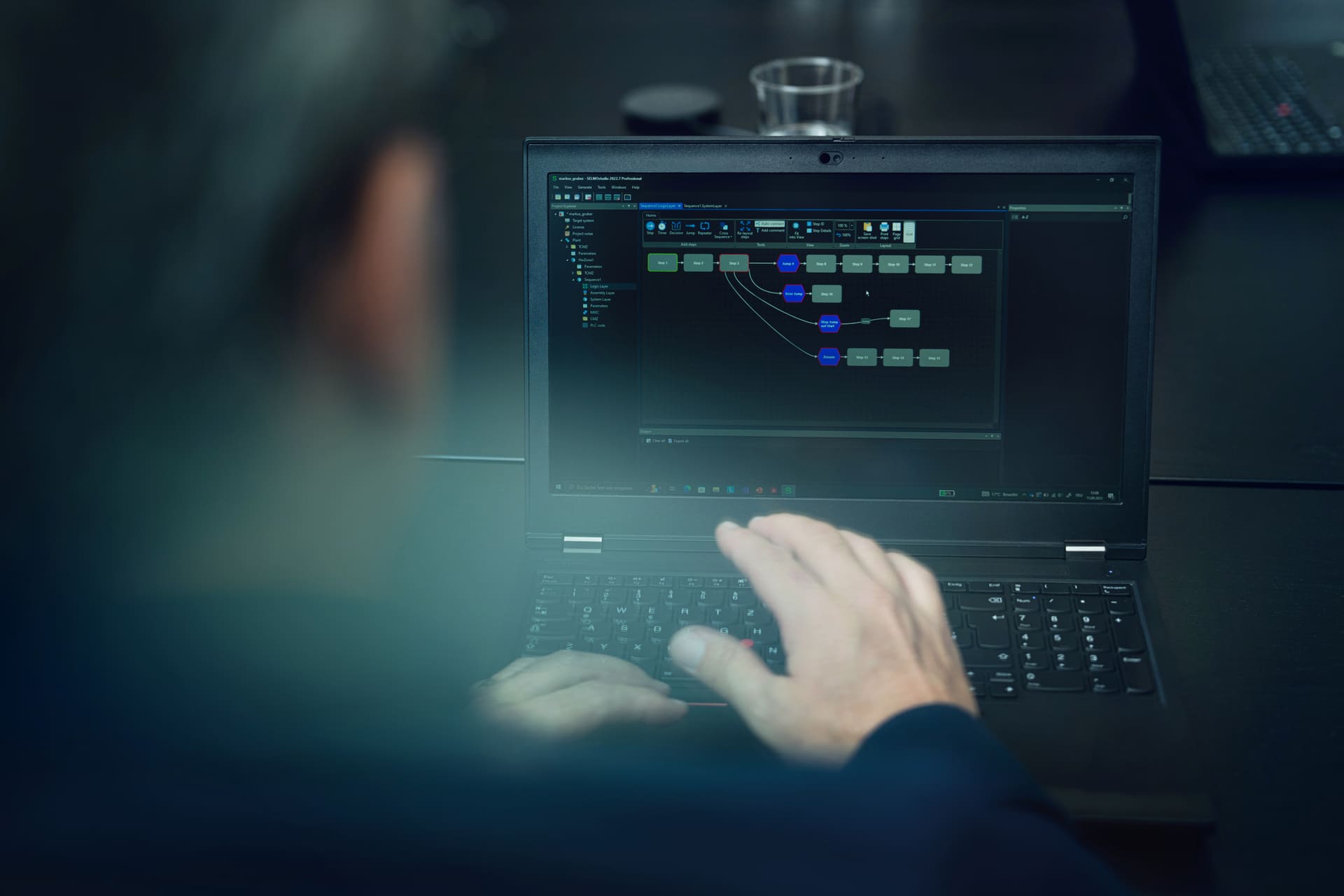
Solution
The automated creation of the PLC programs by describing the machine behaviour with the Selmo method.
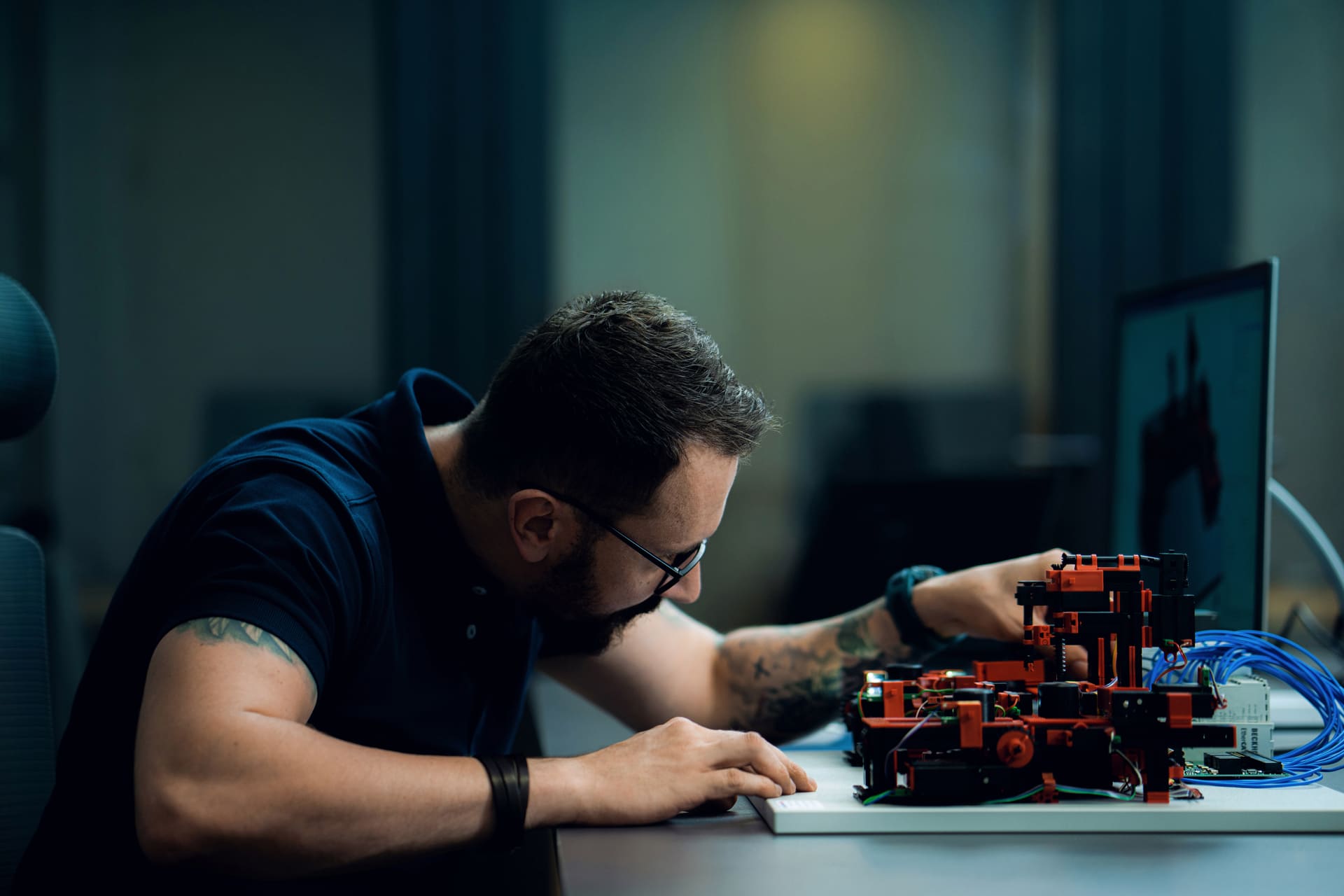

Initial situation & challenges
"For the control, drive and safety technology, we use the hardware of all established manufacturers," explains Christian Wilfing, automation engineer at Brunner Automation. "We can't always choose the make ourselves as the customer often specifies it."
The resulting diversity is a hurdle for software creation and commissioning. Automation engineers must be familiar with different systems and varied development environments. In addition, they have to program many parts of the programme several times due to the various platforms preferred by their customers. This also increases the effort for software testing and commissioning.
In addition, the continued success of Brunner Automation has created a growing need for PLC programmers, both for the initial creation of machine software and for software maintenance and troubleshooting. Since these skilled workers are in high demand and, at the same time, hard to find, Stefan Knöbl looked for more efficient ways to design software and make the commissioning and maintenance more effective.
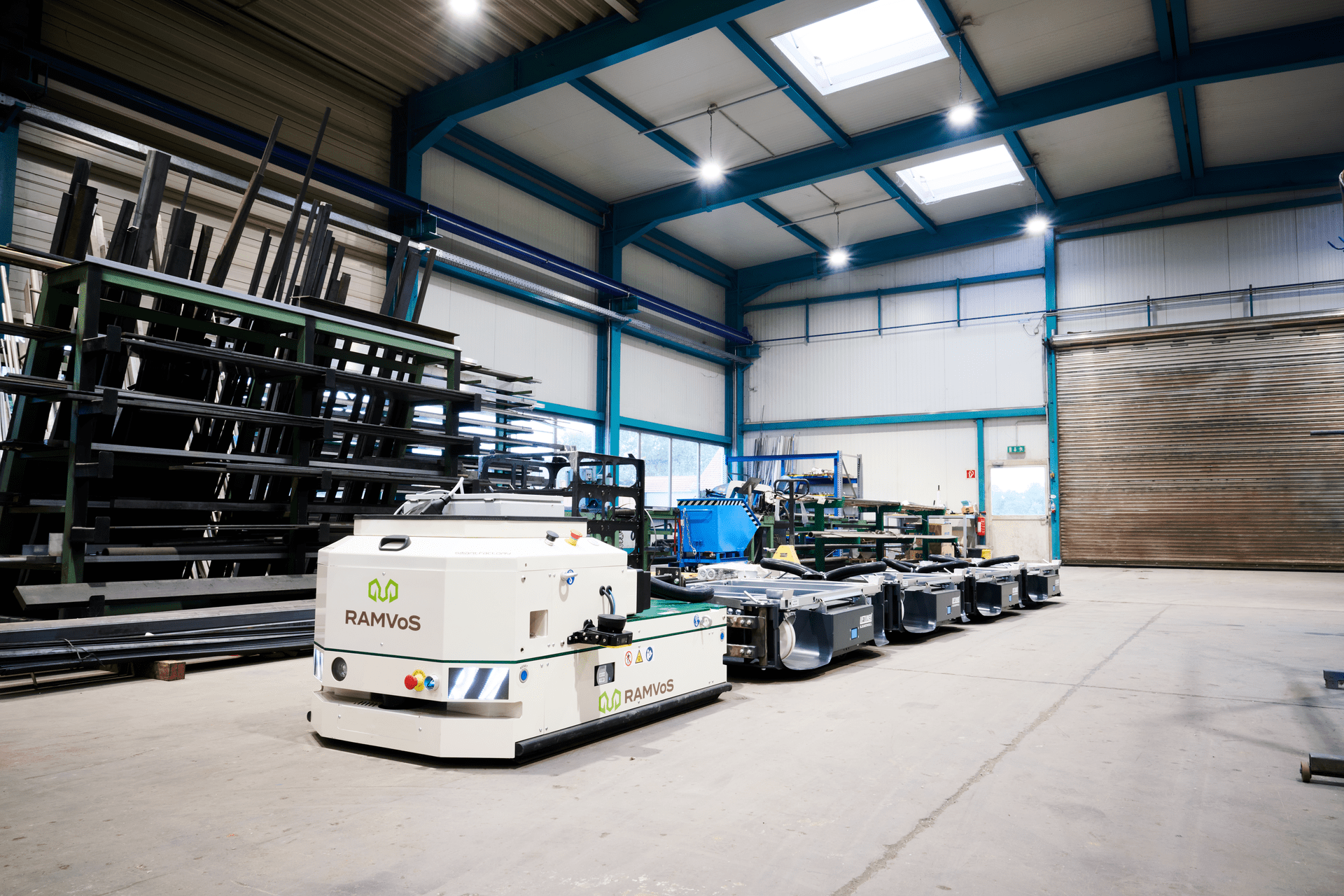
Implementation with Selmo Solution
The first project implemented with the Selmo method is a plant for producing rolling shutter gates at Zeman Bauelemente Produktionsgesellschaft GmbH. Trapezoidal profiles are produced directly from the aluminium sheet coil on a roll former. In the extension supplied by Maschinenbau Brunner, these profiles are fitted with additional components, linked together to form a door leaf of defined length, wound onto a core and finally packed.
At a kick-off meeting, the PLC programmes for a conveyor system were created, ported to a PLC and the virtual commissioning of the system up to a fault-free test run. The basis for this was their CAD models and a verbal process description. The task was completed within just three hours.
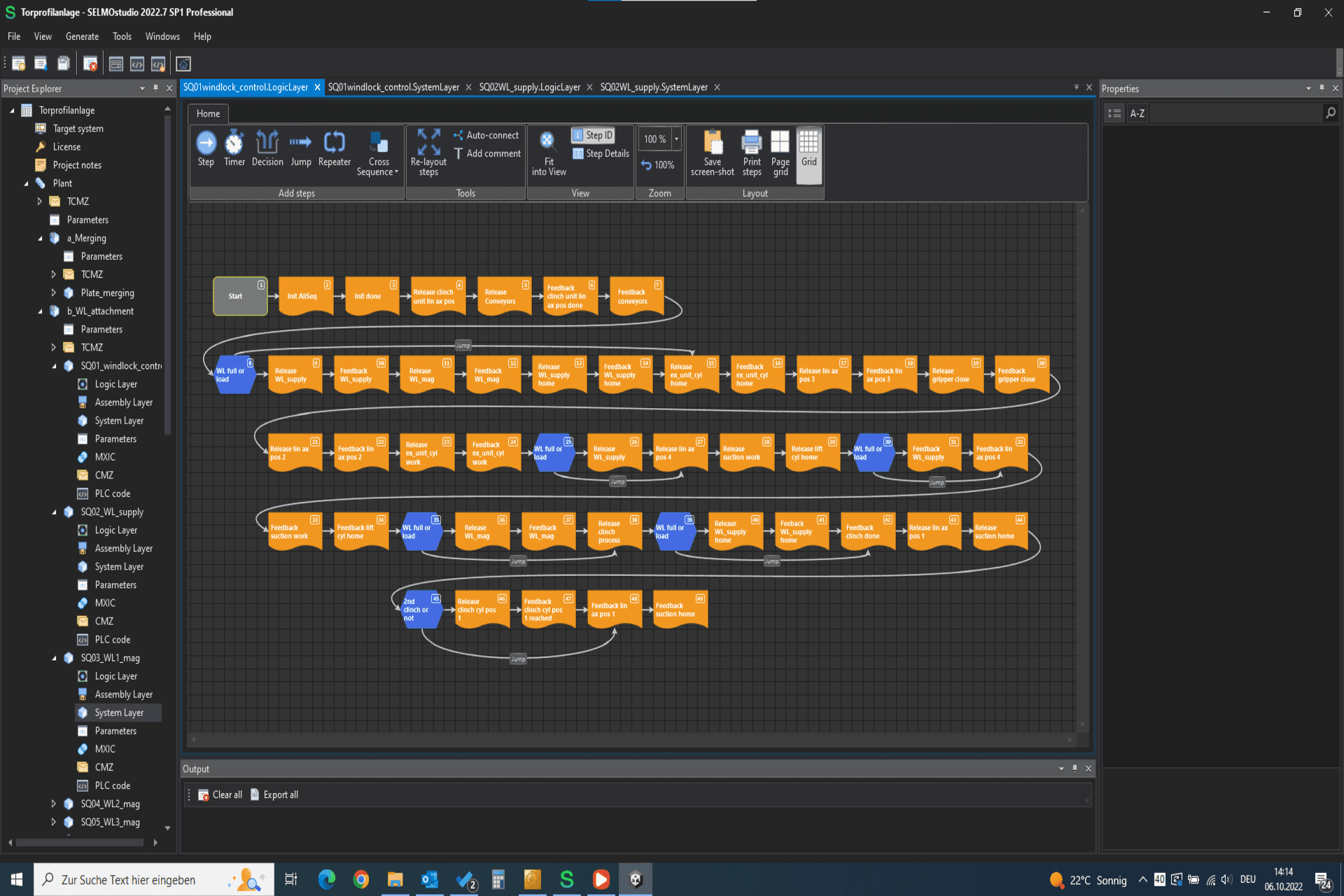
The result: "Very quickly productive"
"The Selmo Solution eliminates the translation of machine behaviour into sequential instructions as an intermediate mental step," emphasises Christian Wilfing. "The lines of code are created automatically, and you can concentrate on creating core elements such as process steps and jumps." In the process, many errors known from classic PLC programming get caught early because, for example, collisions can be avoided very easily by defining blocking conditions. As a result, the automation experts at Brunner Automation managed to switch from classic PLC programming to the Selmo method in less than three weeks, and this was without any training.
In general, the switch to the Selmo method contributed a lot to saving time. In addition, virtual commissioning, which includes the entire drive technology, also contributes to this. "With the Selmo method, we managed to get started at a higher level," Stefan Knöbl confirms. "It saved us much basic work, estimated at one month."
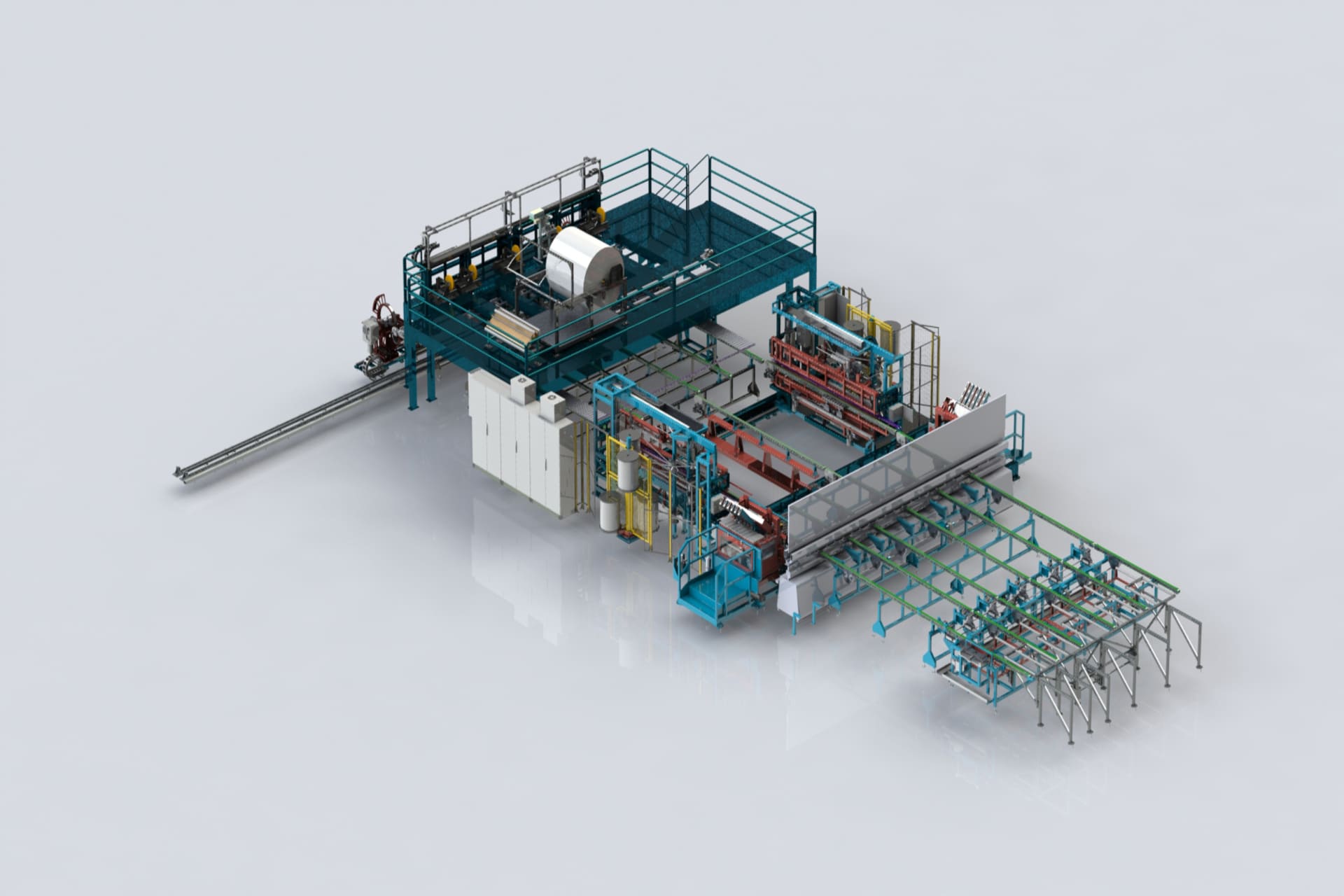